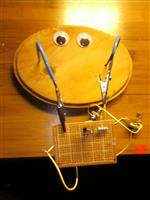
I've got a PCB with a standard HD44780 based LCD on one side.
I've typically used four M2 screws with four 8mm standoffs and nuts, and have used split-ring lock washers along with flat washers on the nut side of the connection:
screw head -- flat washer -- PCB -- standoff -- LCDPCB -- flat washer -- split washer -- nut
It's not failing me (high vibration environment) but I'm wondering if I'm applying this correctly. Some people absolutely hate on split ring lockwashers while others say they work fine. I tend to be in the latter camp since I don't recall ever having to tighten or replace one with any repairs that have come back, but if there's a better way I'm happy to learn.
- Comments(1)
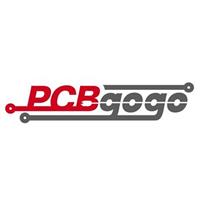
A****min
Dec 19.2019, 18:03:28
Its a known problem that epoxy/FR4 PCB material tends to cold flow under high local pressure. Therefore the spring washers are performing an important duty of maintaining acceptable clamping pressure even if the PCB gives a little bit. You need the flat washers to distribute the load and prevent the spring washers digging in so there is no way of simplifying this assembly.
It sounds like its goode enough but if you think you need better, a drop of threadlocker on each nut might be a possible improvement. However, if it is assembled in a confined enclosure before the threadlocker is fully cured, vapours may haze a plastic display window. Another option would be to switch to Nylock nuts, keeping everything else the same.