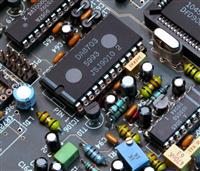
BGA, standing for Ball Grid Array, is an advanced type of surface mount technology applied to ICs. It is usually used to permanently mount the devices such as microprocessors. BGA has many ball-shaped bumps on the underside of the package to provide interconnect points that meet the requirements of high-density packaging. Its short average trace length and sufficient soldering space make it an ideal package for high-density, high-speed devices.
Figure 1: BGA package
Types of BGA
1. PBGA (Plastic BGA): It is generally a multi-layer board composed of 2-4 layers of organic materials.
2. CBGA (Ceramic BGA): As the name suggests, it has a ceramic substrate. The electrical connection of the chip to the PCB is usually via FlipChip (FC).
3. FCBGA (FilpChipBGA): It is a hard multi-layer substrate.
4. TBGA (TapeBGA): The substrate is a strip-shaped soft 1-2 layer PCBs.
5. CDPBGA (Cavity Down PBGA): It refers to the chip area with a square low depression in the center of the package . (also known as the cavity area)
Figure 2: BGA package structure
Benefits of BGA
1. Small size with large storage
BGA is famous for its ultra-fine pitch technology and high-density interconnection. Compared to other types of SMT packages, BGA only takes one-third of the space with the same storage capacity.
2. Great electrical performance
The BGA pins are very short with the leads being replaced by solder balls, which shortens the transmission path of various signals, reduces the lead inductance and capacitance, and thus enhances the electrical performance.
3. Great heat dissipation
The contact surface between the ball contact array and the PCB is large and short, which offers better heat dissipation and prevents the device from overheating.
4. High reliability
BGA has a great coplanarity. The solder balls are not all aligned with respect to the seating plane and tolerance for this misalignment is allowed.
Disadvantages of BGA
1. Hard to inspect after soldering
X-ray inspection is the only option used to ensure the reliability of the solder connections while this inspection technique is time-consuming and expensive, requiring well-trained and experienced operators.
2. Hard to rework
During the maintenance of BGA components, engineers need to protect the solder balls while cleaning the solder paste. When a single solder joint is damaged, the entire BGA must be removed, and the removed part cannot be reused.
Figure 3: Rework on a BGA package
3. High requirements on the storage environment
BGA components are quite sensitive to changes in temperature and humidity. The ideal storage temperature is 20 to 25 degrees, and the humidity is less than 10%. Meanwhile, special attention should be paid to electrostatic protection.
Quality inspection of BGA
BGA components may encounter different defects after soldering resulting from assembly equipment, operating environment, and soldering techniques. Common BGA defects include misalignment, loose solder, opens, cold solders, bridges, shorts, and cavities. In addition, BGA solder balls may also have problems with missing or dropped and non-uniform sizes. At present, Electrical test, Boundary scan inspection, and Automated X-ray inspection are the most commonly used BGA testing techniques.
1. Electrical test
As the most traditional quality testing method, the Electrical test is mainly used to find open circuit and short circuit defects.
2. Boundary scan inspection
Boundary scan technology relies on the inspection port of the boundary scan design, which can access every solder joint on the boundary connector so as to inspect the opens and shorts on components.
3. Automated X-ray inspection
The two inspection techniques discussed above can only test the electrical performance of the package, while unable to detect the soldering quality. After soldering, BGA components are completely covered by the components, for which solder connections are not visible. The popular AOI technique is unable to inspect hidden connections underneath BGAs. Automated X-ray inspection is thus developed which can check the solder joints under components and show defects in solder joints such as voids and bubbles that may not be visible with AOI.
Figure 4: Defects detected by X-ray machines
The main working principle of X-ray detection relies on X-ray penetration. Substances of different densities such as solders, components, and PCB substrates would present different light intensities when penetrated by X-rays depending on their atomic weights. This intensity contrast forms a radiographic image, facilitating the detection of internal defects in the package. X-ray inspection will not cause damage to the internal structure of the package while maintaining high accuracy of detection outcomes.
Figure 5:Automated X-ray inspection machines in PCBGOGO factory
Conclusion
As electronics products develop towards miniaturization with more advanced functions, the BGA package has become a popular option due to its ultra-fine-pitch technologies and reliable high-density interconnection. To ensure its quality, a combination of Electrical test, Boundary scan inspection, and Automated X-ray inspection should be conducted during the assembly process. PCBGOGO is a professional PCB and PCB assembly manufacturer with vast industry experience. Their fully automated SMT lines with advanced testing machines ensure the precise and quality consistency needed for BGA packages. Contact them today if you have BGA assembly needs.