
Ok, I have satisfactory method for hand printing solder paste and reflow soldering for my prototype lab. I have done my first real board on that, and my process definitely needs some development.
First, placing the stencil could be easier, but I don't think that is a real problem. My next board will have two small holes on the PCB and on the stencil in opposite corners. Then I'll put same size of pegs trough the holes and tape the stencil down. That should do it. Of course, if you have a better idea, please share! but it was still a chore. The board had 460 components, and besides a couple of connectors, all SMD. For this old guy, that took way too long and became difficult towards the end. My hand started shaking (not much, but with SMDs, you don't want any!) after an hour or so, with two more hours to go. The paste also started going dry (the final board turned out to be fine, though). Definitely something that I'm not looking forward doing again!
Right now, I can't think of anything to improve the manual method. Thank you Mike! You have more or less perfected manual already. Or is he? If you have any tips, hints or ideas, please share!
And I can't help thinking about a machine for this. A hobbyist/prototype pick and place machine could be very simple, basically doing what the manual method does. No automatic feeders are needed. I envision guide slots with the part strips (equivalent of those cardboards (see the video)) and for this purpose, it would be perfectly ok if the control program would do first 40 (or whatever length of the slots are) bypass caps and then ask "please peel 24 more from slot 1". Also, it would be ok if the control program says "First tray finished. Please reload slots: Slot 1: part type xxx (470pF, 0805 capacitor) 24 pieces. Slot 2: ...." The ICs or special components I could place by hand, if the 400+ chip parts would be done by a machine. Or maybe place them pre-oriented to a jig or something.
I would think that with something like this, the 4-5 hours of assembly (with preparation of those cardboard plates) would have been less than one. Not good enough for about any level of production, but a tremendous help for hobbyist or a prototype lab. Not to mention the easy part of it...
I searched, and found some videos and info for DIY projects, but none documented enough to just build one. On the other hand, the videos show that in principle, something like that is feasible. I didn't find any affordable commercial units. Seems to me that this only needs a simplest CNC machine, modified head unit and some software. This project would not pay back to me in time, but it would be so fun.
So, why should't I? Ideas? starting points? Or if you know something like the above commercially available (say, less than 1000€), let us know, too.
- Comments(1)
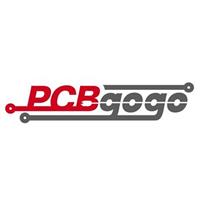
A****min
Feb 19.2020, 18:06:47
First you need some kind of tool mount moving in XY plane. Since pick and place doesn't involve significant force, this can be one out of steel or aluminum rods and extrusions. For linear slides you have a few options: furniture drawer sliders (cheap, available), supported or unsupported hardened rods+ linear bearings, linear slides (expensive) or diy kind usually made of some angled extrusions and ball bearing. Either of those can do the job. As for drive system since you want rather fast movement of the placement head, I would go with stepper motors + gears + toothed belt. This provides fast movement, at cost of small force (which is completly fine for this application). Also without significant reduction ratio resolution is relatively small (half inch toothed wheel with 200steps/rev motor gives you 0.4mm resolution, but when you get use a microstepping driver with 1/16 division ratio you can get something like 0.025mm which is acceptable.
That's for XY movement. As for Z movement you need some way to adjust height of nozzle over the PCB. For placing identical parts that can be done manually (eg. separate setting for resistors and capacitors) but automatic adjustment can also be done. i think that ordinary threaded rod with a nut driven by a stepper will do the job. there has to be some kind of shock absorption between the nozzle end and whole machine (maybe some kind of spring). Of course you need to have a vacuum supply and a nozzle.
You need some kind of optical recognition or a few lost steps will cost you dearly. Open loop solutions are not the best way here. You also need to take into account that parts can move a little inside the reel.
On top of that moving parts have to be as light as possible, in order to allow rapid accelerations without vibrating.