
I'm doing a design which will carry 70 A. Having decided that putting wires in would be a waste of time as the thing need potting meaning the wires would need to be longer than necessary and then cut down to size and of course you only have one shot at it. I was going to use 6 16 gauge wires but have instead decided to use a threaded stud which should make assembly easier and quicker and be more flexible for the end user.
So I have created pads on my board with a 4 mm diameter hole and an 8 mm diameter exposed copper. The plan would be to have a screw through from the bottom of the board a brass tube from the board up to the height of the potting compound and then a nut and washer so that the screw clamps across the board and the brass tube. Obviously it would make electrical sense that the brass tube is soldered down to the board. But the best way of doing this would be to have it soldered in the reflow oven along with every other component. But as far as I know to do that it would be necessary to "pick and place" the brass tubes. Is this something feasible or was it be quite the manual operation?
I'm hoping this solution would be a lot easier and quicker and cost-effective than trying to solder in many wires as with a large copper planes this would be a hard job to do manually.
- Comments(1)
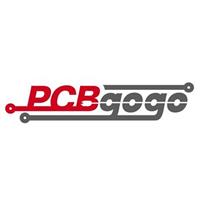
A****min
Jan 15.2020, 10:13:07
Whilst everything is possible, it is unlikely that a feeder can be found for the SMD PnP robot for the brass tubes.
If the tube is a tight fit in the hole, then pushing them in by hand before loading the rest of the SMD components would probably be the best method. BUT the PnP robot will need programming to ensure its head does not collide with the brass tubes.
An alternative might be to have the tubes exit through the bottom side of the board. You can then make a holding tool with female holes in it to allow the male brass tubes to "sit inside the holes". This ensures the PnP placing head cannot collide with the tubes.
Yes, this would certainly save time. I would suggest making a thicker (at least 8 thousands-of-an-inch) solder paste stencil to ensure you lay down enough paste for a good joint.
You will need plenty of heat in the reflow oven. Consider pure copper tubes instead of brass. These conduct both electricity & heat much better than brass & will expand & contract at the same rate as the copper on the board.
If the copper/brass tube is malleable enough, you could make up a peening tool to actually peen each end/one end of the tube over the pad.
Depending on the diameter of the tube, wave soldering may mainly fill the tube with solder if the SMD side is left open to the air. If the solder paste covers the top of the tube, the resultant air-lock will likely prevent the tube filling with solder.
Bit of both - depending on the assembly process of your manufacturer you can have a manual manipulation step - for instance we had some obscure connectors that had to be placed by hand and there was no problem with that. They just first put on the solder paste, then put it through the pick and place machine, then hand placed the nasty parts and then put it into the oven. It didn't really increase the cost that much.
Your manufacturer should have something similar.
Also, if you are out for cost, you might want to consider sheet metal cutouts rather than tubes and similar - cutting out a "line" from sheet metal via waterjet costs very little and you can create pretty much any shape you want.